NMP赛道依旧火热 高端市场供应能力不足
近年来,新能源汽车产业发展迅速,带动了锂离子电池市场的扩大。作为锂电池关键化学品的聚偏氟乙烯(PVDF)及配套溶剂N-甲基吡咯烷酮(NMP)吸引行业关注。
生产及应用
根据生产工艺的不同,NMP分为合成料与回收料。
其中,合成料是指采用 BDO合成路线,合成γ-丁内酯,γ-丁内酯再与甲胺反应生成的NMP产品。
根据反应条件不同,合成反应可分为无催化反应与催化反应,前者是大多数生产企业采用的生产工艺。国内仅有迈奇化学的NMP生产采用催化工艺,其自主研发的一种新型分子筛ZSM复合稀土铈催化剂,能有效加快中间体NMH闭环的速度。
回收料则是指采用动力电池生产厂商使用后的NMP废液回收给NMP生产厂商,对回收的NMP进行物理提纯。作为溶剂使用的NMP,绝大部分都可以回收再利用,既能节约成本又能减少对环境的影响。随着国内动力电池产量的快速增长,NMP的回收提纯市场发展迅猛。
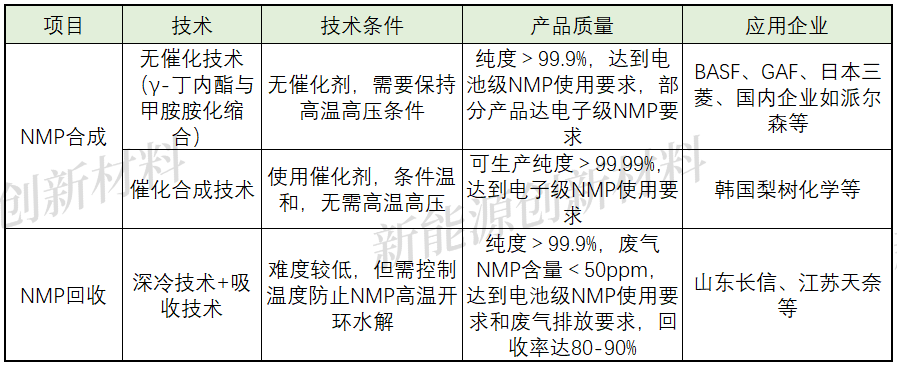
资料来源:观研天下
NMP在锂电行业主要运用在配料和涂布阶段。
配料阶段:作为PVDF溶剂,参与浆料分散,形成介质均匀,在一定粘度范围内长时间保持稳定的浆料。
涂布阶段:担造孔功能,NMP以稳定的速度从湿膜中挥发,形成孔径均匀,分布均匀的多孔微电极结构。正极涂布烘干有机溶剂后会产生含NMP尾气。NMP回收的场景主要在于涂布尾气处理和后续NMP提纯回收。
NMP尾气目前主要处理工艺有:冷凝+蜂巢式转轮吸附、冷凝+水喷淋和多级水喷淋。
冷凝+吸附工艺:先将涂布尾气冷却,收集其中的大部分的NMP,再通过吸附转轮将尾气处理至达标,同时脱附的尾气返回前端。
水喷淋工艺:利用NMP水溶性佳的特点,采用水吸收NMP,从而使尾气达标排放。
各工艺均有其适用范围和优劣势,需要根据实际生产情况和工程经验进行选择。当NMP从尾气转移自水溶液或冷凝成液后就形成NMP废液,其纯度往往达不到电池生产的要求,需要进一步提纯后才能回用。
NMP废液中一般含有NMP、水、胺类等其他有机杂质,由于电池级NMP直接用于电极制作,为保持电池一致性对纯度要求极高,因此对回收的纯度要求严格。
供需现状
目前国内竞争主要是直接生产厂家和回收提纯厂家以及小部分进出口贸易商之间的竞争,回收提纯厂家占据分散的客户群和低端市场,直接生产厂家则占据主力客户群和高端市场。
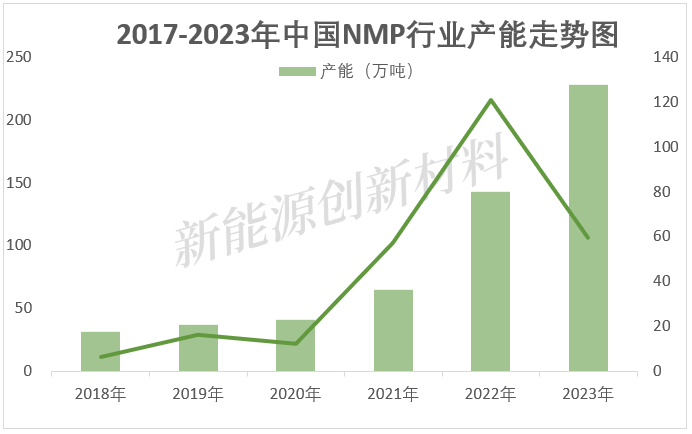
根据研究报告数据显示,2023年国内锂离子电池出货量887.4GWh,同比增长35.27%,其中动力电池是我国锂电池最大细分品类,2023年占比71.11%。而按每GWh锂电池需要1700吨NMP吨测算,2023年我国锂电池NMP需求量约为150.86万吨。
新增产能统计 目前,我国主流NMP生产工艺为无催化剂合成方法,增产周期较短(一般扩产周期在1-2年),进入门槛较低。近几年,受下游锂电池行业快速发展,从事NMP生产、回收的企业数量逐渐增多。 不过,随着NMP产能不断扩张,其发展结构失衡问题也随之增加。其中,中小型企业数量众多且以回收为主,而技术水平低致低端产能过剩,但高端产能仍然较低。例如,市场对超净高纯NMP要求≥99.9%,水分含量要求≤0.01%,所以大部分国产企业无法大规模生产。 2023-2025年我国NMP新增产能建设情况 未来发展 N-甲基吡咯烷酮(NMP)以其特有的无毒性、沸点高、极性强、粘度低,腐蚀性小、溶解度大,挥发性低、稳定性好的性质作为生产锂离子电池电极非常重要的辅助材料,在锂离子电池前段配料过程中最普遍被使用,在锂电池的整个生产过程中起着非常重要的作用。 未来行业发展趋势如下: 1、产业链配套模式,实验新工艺生产。目前中国NMP大部分是GBL法生产,而GBL是以BDO为原料配套生产,BDO上游可以追溯到顺酐和正丁烷。虽然此条产业链较长,但是正丁烷是目前炼化企业需要重点关注产业链延伸的产品。如果企业能够实现从正丁烷模式的下游配套生产,NMP将会极具有产业链优势。 2、产能扩张,竞争激烈。NMP未来拟在建项目众多。未来数年内,中国NMP的市场体量将会实现翻倍。所以,巨大的市场新增体量必然带来短期的供应过剩风险,市场竞争也将升级。 3、下游消费未来仍在高速增长。但是,供应端的增速要明显快于消费市场,这也是行业内对于NMP的下游领域更加看好所致。在这样的背景下,预期中国NMP的供需矛盾将会明显失衡,具有产业链优势和在主要消费市场的NMP生产企业,或将更有市场竞争力。 文章来源:新能源创新材料编辑整理